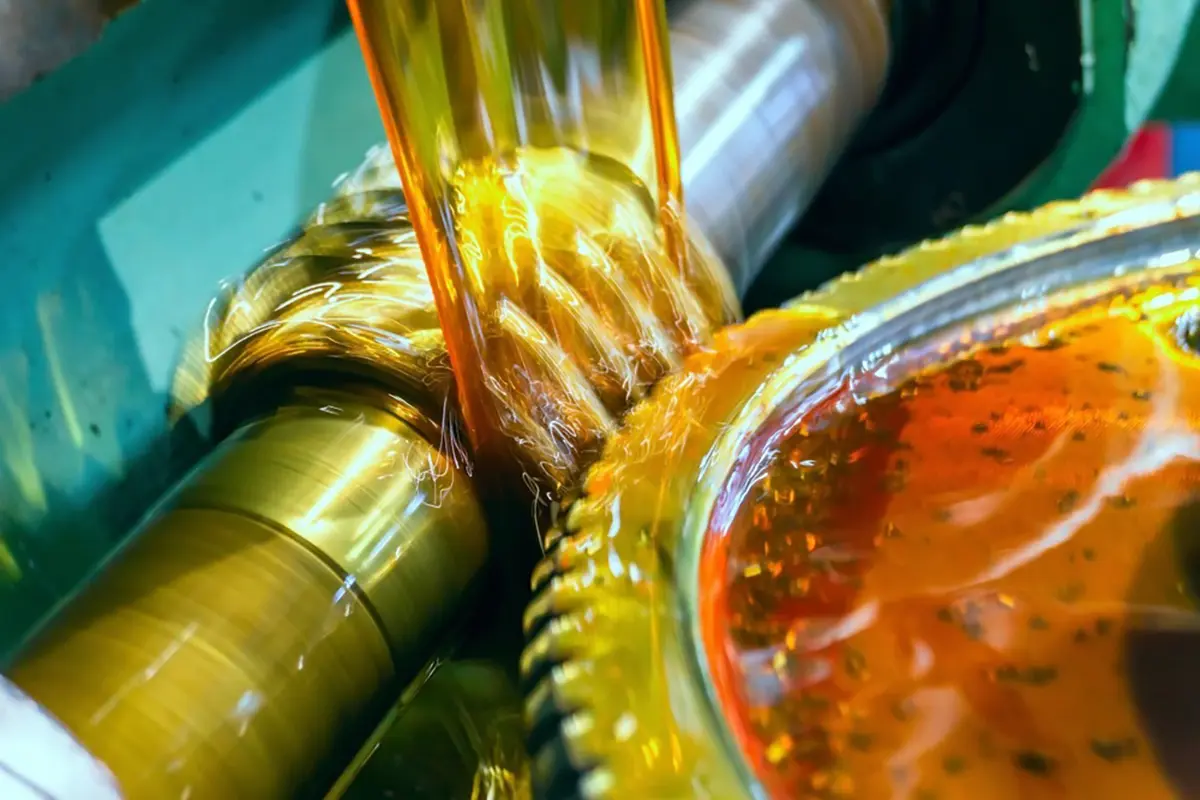
آلودگی روانکار، عامل پنهان اما اصلی در خرابی ماشینآلات
فهرست مطالب
این آلودگی، حتی در مقادیر بسیار کم، میتواند آسیبهای جدی به اجزای حساس دستگاه وارد کرده و در نهایت منجر به توقف های غیرمنتظره و پر هزینه شود.
دلایل اهمیت موضوع
تحقیقات میدانی و تجربیات عملیاتی نشان میدهند که بخش قابل توجهی از خرابیهای تجهیزات مکانیکی به روانکاری نادرست یا روانکار آلوده مربوط است. در بسیاری از صنایع، بیش از ۷۰ درصد خرابیهای سیستمهای چرخشی و هیدرولیکی به نحوی با روانکار مرتبط هستند. بخشی از این آسیبها ناشی از کیفیت پایین روغن مصرفی نیست، بلکه به دلیل ورود ذرات ناخواسته و آلاینده به روانکار رخ میدهد.
منابع آلودگی روانکار
آلودگی روانکار ممکن است از دو منبع اصلی ناشی شود: آلودگی خارجی و آلودگی داخلی. در حالت اول، عواملی مانند گرد و غبار محیط، رطوبت، ذرات فلزی معلق، شن و حتی میکروارگانیسمها میتوانند از طریق باز کردن درب مخازن، نشتی در سیستم، یا تنفسگیرهای ضعیف وارد روانکار شوند. در حالت دوم، آلودگی از داخل سیستم بهوجود میآید، مانند ذرات فلزی حاصل از سایش قطعات، اکسیداسیون روغن، و تخریب افزودنیها.
حتی روغنهای تازه خریداری شده نیز لزوما پاک نیستند. در واقع، فرآیندهای تولید، حمل و ذخیرهسازی روانکارها میتوانند منبع آلودگی باشند. در بسیاری از موارد، روانکار تازه از لحاظ تعداد ذرات، چندین برابر بالاتر از سطح تمیزی مورد نیاز تجهیزات حساس است.
اثر آلودگی بر عملکرد تجهیزات
وقتی روانکار آلوده وارد سیستم میشود، تاثیر آن بلافاصله قابل مشاهده نیست. اما در طول زمان، ذرات ریز موجود در روغن میتوانند باعث خراشیدگی سطوح تماس، افزایش سایش، و ایجاد خستگی در قطعات شوند. در یاتاقانها، پمپها و دندهها، این فرسایش میتواند به ترک، شکست و در نهایت از کار افتادن سیستم منجر شود. از سوی دیگر، آلودگی آب میتواند باعث جداسازی فازها، رشد باکتریها، و کاهش خاصیت روانکاری شود.
افزایش دمای موضعی ناشی از اصطکاک بیشتر نیز یکی دیگر از پیامدهای روانکار آلوده است. این موضوع منجر به تسریع در تجزیه شیمیایی روغن، تولید اسیدها و لجن، و در نتیجه تخریب بیشتر سیستم میشود.
راهکارهای پیشگیری و کنترل آلودگی
برای مقابله با این خطر پنهان، باید از یک رویکرد جامع استفاده کرد که شامل چهار بخش اصلی است: جلوگیری از ورود آلودگی، حذف آلودگی موجود، پایش مستمر و مدیریت صحیح روانکارها.
۱. جلوگیری از ورود آلودگی:
نخستین گام، جلوگیری از ورود آلودگی به روانکار است. استفاده از سیستمهای بسته برای نگهداری روغن، قیفهای مجهز به درپوش، و فیلترهای تنفسگیر موثر میتواند ورود گرد و غبار و رطوبت را به حداقل برساند.
۲. حذف آلودگی:
فیلتر کردن روغن پیش از ورود به سیستم، یا حتی فیلترگذاری مداوم در حین کارکرد ماشینآلات، باعث حذف ذرات معلق میشود. انتخاب فیلتر مناسب با اندازه منافذ دقیق (مطابق با حساسیت تجهیزات) اهمیت زیادی دارد.
۳. پایش وضعیت روانکار:
استفاده از آنالیز روغن و پایش دورهای سطح آلودگی، به مدیران تعمیرات کمک میکند تا پیش از بروز خرابی، نسبت به رفع مشکل اقدام کنند. شاخصهایی مانند شمارش ذرات، سطح رطوبت، گرانروی و اسیدیته روغن از جمله پارامترهایی هستند که باید بهطور مستمر کنترل شوند.
۴. مدیریت روانکار:
ذخیرهسازی مناسب، آموزش پرسنل، برنامهریزی برای تعویض به موقع، و ثبت سوابق مصرف و آلودگی میتواند به شکل چشمگیری از خرابیها پیشگیری کند. علاوه بر این، تدوین دستورالعملهای مشخص برای انتقال، فیلترگذاری و استفاده از روانکارها نیز در این زمینه حیاتی است.
نتیجهگیری
آلودگی روانکار، عاملی خاموش ولی تاثیرگذار در کاهش عمر ماشینآلات و افزایش هزینههای نگهداری است. با وجود پیشرفت تکنولوژی، بسیاری از خرابیها هنوز به دلیل بیتوجهی به کیفیت روانکارها اتفاق میافتند. با اتخاذ یک رویکرد پیشگیرانه و سیستماتیک، میتوان از وقوع بخش عمدهای از این خرابیها جلوگیری کرد، بهرهوری تجهیزات را افزایش و هزینههای عملیاتی را کاهش داد.
جهت مطالعه بیشتر به منبع این نوشته مراجعه نمایید.
دیدگاهتان را بنویسید
تاکنون دیدگاهی در این مطلب ارسال نشده!