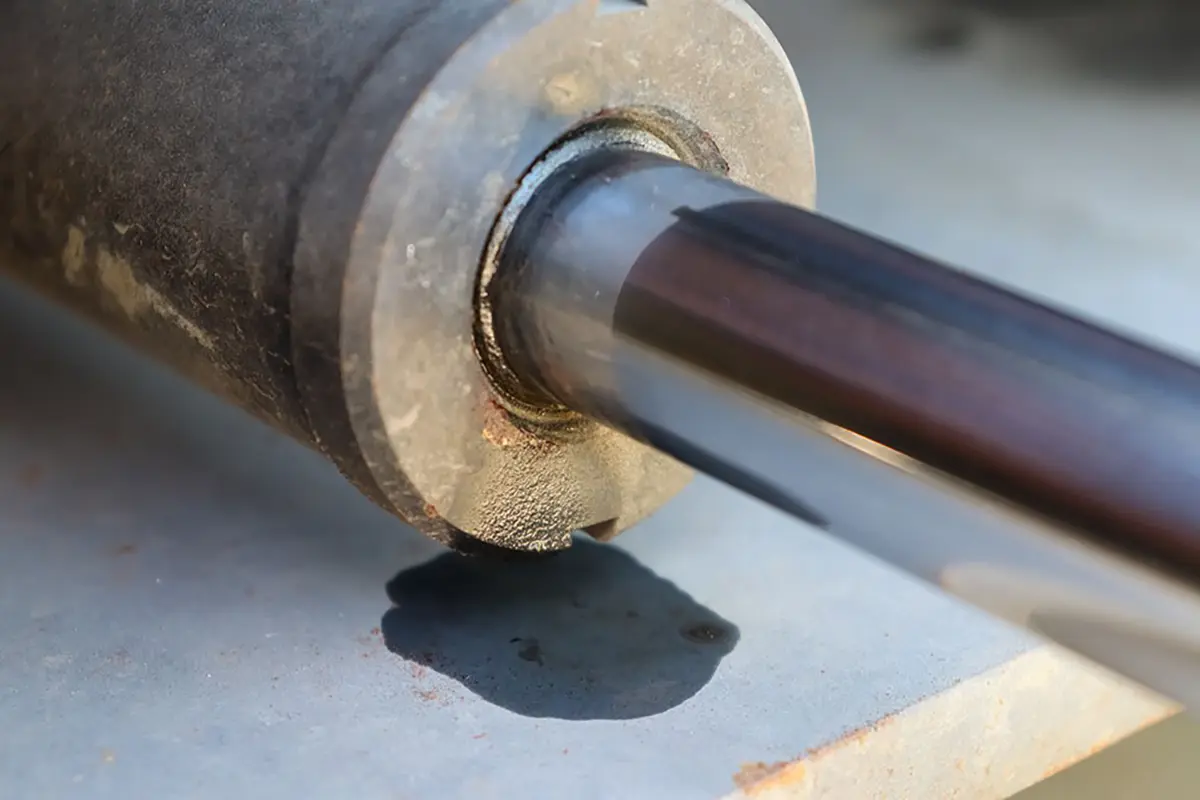
مدیریت نشت روغن هیدرولیک؛ راهکاری برای کاهش هزینه در صنایع سنگین
فهرست مطالب
در تلاش برای کاهش هزینهها، برخی شرکتها به استفاده از روغنهای ارزانقیمت روی میآورند. اما این انتخاب میتواند نتیجهای معکوس داشته باشد و باعث افزایش مصرف روغن و استهلاک زود هنگام ماشینآلات شود. در واقع، هزینههای پنهانی که از نشت روغن ناشی میشود، به مراتب بیشتر از صرفه جویی اولیه در خرید روانکارهای ارزان است.
چگونه نشت روغن را مدیریت کنیم؟
برای کاهش اثرات مالی و فنی ناشی از نشت روغن هیدرولیک، اتخاذ یک رویکرد جامع و سیستماتیک در نگهداری و نظارت بر سیستمهای هیدرولیک ضروری است. این رویکرد در سه مرحلهی کلیدی خلاصه میشود:
1. شناسایی و فهرست برداری از سیستمهای هیدرولیک
نخستین گام در این مسیر، شناسایی تمام سیستمهای هیدرولیک موجود در کارخانه و ثبت مشخصات آنها است. این اطلاعات شامل محل قرارگیری، ظرفیت مخازن و نوع تجهیزات متصل به هر سیستم میشود. با نصب ابزارهای اندازهگیری بر روی مخازن روانکار، میتوان مقدار روغن تزریقشده یا مصرفی را در هر مرحله ثبت و پیگیری کرد. این کار دید روشنی از وضعیت مصرف در اختیار مدیریت میگذارد.
2. بررسی و تحلیل میزان نشت روغن
پس از طبقهبندی سیستمها، لازم است میزان نشت روغن در هر واحد بهصورت دقیق اندازهگیری شود. برای این منظور، باید حجم روغن مصرفشده در طول زمان را نسبت به ظرفیت هر سیستم بررسی کرد. این اطلاعات به شناسایی واحدهایی کمک میکند که مصرف غیرعادی دارند و احتمالا دچار نشت هستند.
بهطور معمول، کارخانهها دارای میزان نشت مشخصی هستند، اما زمانی که مصرف از یک سطح مشخص فراتر میرود، نشانهای از وجود ایراد در تجهیزات یا اتصالات است. شناسایی این نقاط ضعف، فرصت مناسبی برای مداخله پیشگیرانه فراهم میکند.
3. بازرسی و پایش مستمر
پس از شناسایی واحدهای مشکلدار، لازم است بازرسیهای تخصصی مانند بررسیهای فرابنفش یا صوتی انجام، تا منبع دقیق نشت مشخص شود. این بازرسیها باید به شکلی صورت گیرد که خللی در روند تولید ایجاد نکند و تعمیرات به موقع انجام شود.
همچنین پایش مستمر مصرف روغن در طول زمان و مقایسه آن با مقادیر خریداری شده، شاخص روشنی از کارایی اقدامات نگهداری ارائه میدهد. با ادامهی این روند، میتوان روند بهبود را ارزیابی کرده و در صورت نیاز اصلاحات بیشتری انجام داد.
صرفهجویی واقعی در مصرف، نه صرفا کاهش هزینه خرید
یکی از اشتباهات رایج در میان مدیران کارخانهها، تمرکز صرف بر هزینهی خرید روانکار است. در حالی که هزینههای ناشی از نشت روغن، توقف تولید، تعمیرات اضطراری و کاهش عمر تجهیزات بهمراتب سنگینتر است. رویکرد هوشمندانه، تمرکز بر کاهش مصرف بیرویه و افزایش بهرهوری از طریق نگهداری دقیقتر است، نه انتخاب ارزانترین محصول در بازار.
با اجرای یک برنامه منظم مدیریت نشت روغن، کارخانهها میتوانند تا ۱۰ درصد از مصرف سالانه روانکار خود را کاهش دهند. این صرفهجویی در مقیاسهای بزرگ، به معنای کاهش چشمگیر هزینههای عملیاتی و افزایش پایداری در تولید خواهد بود.
جمعبندی
نشت روغن در سیستمهای هیدرولیک یک چالش رایج اما قابلکنترل است. با شناسایی دقیق سیستمها، اندازهگیری دقیق مصرف و نشت، و انجام بازرسیهای منظم میتوان به شکل موثری از اتلاف منابع جلوگیری کرد. مدیریت نشت روغن، نهتنها به حفظ تجهیزات کمک میکند، بلکه نقش مهمی در افزایش بهرهوری و کاهش هزینههای بلندمدت دارد. این فرآیند، بخشی از یک استراتژی کلان نگهداری است که در نهایت به سودآوری و پایداری بیشتر سازمان منجر میشود.
جهت کسب اطلاعات بیشتر به منبع این نوشته مراجعه کنید.
دیدگاهتان را بنویسید
تاکنون دیدگاهی در این مطلب ارسال نشده!