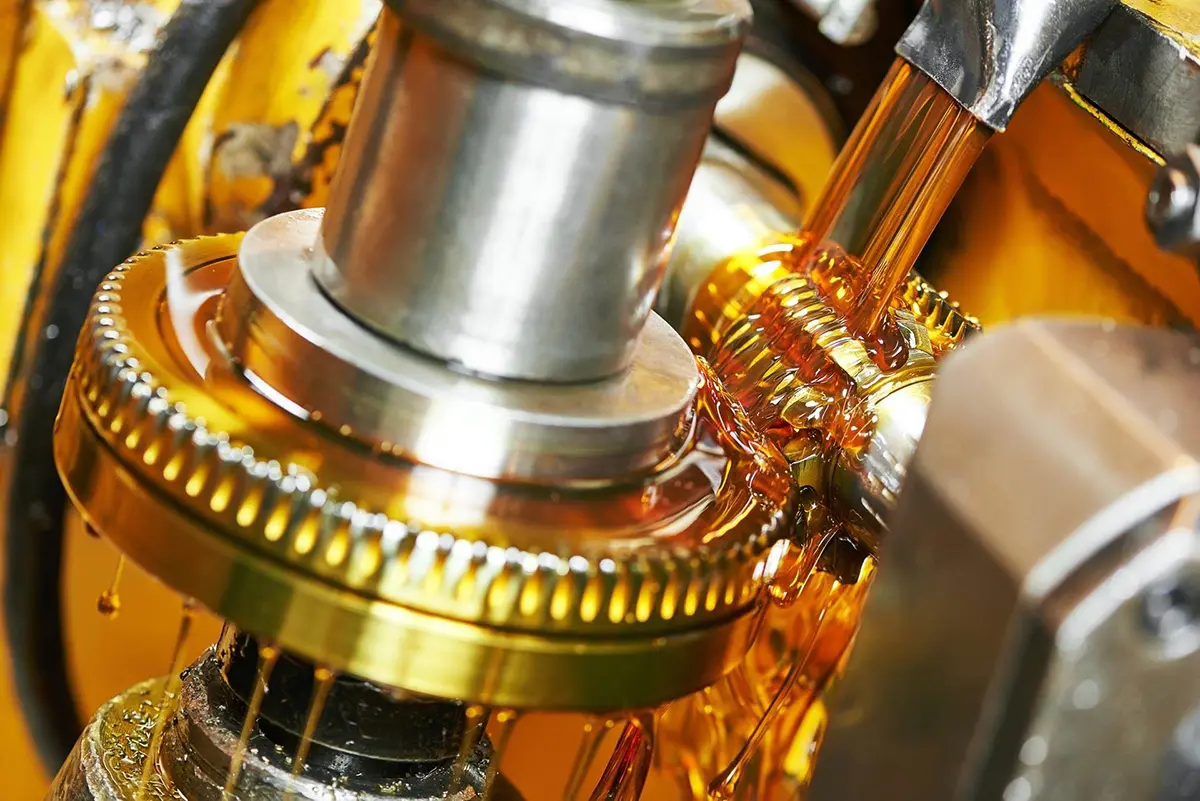
اهمیت تحلیل روغن در نگهداری تجهیزات صنعتی
فهرست مطالب
در صنایع مختلف، حفظ کارایی تجهیزات و جلوگیری از خرابیهای ناگهانی، یکی از مهمترین عوامل موفقیت و پایداری عملیات به شمار میرود. یکی از روشهای موثر در این زمینه، تحلیل روغن است.
این روش به ما امکان میدهد که تغییرات تدریجی در خواص سیالات، میزان آلودگیها و میزان سایش قطعات ماشینآلات را شناسایی کرده و پیش از بروز مشکلات جدی، اقدامات اصلاحی مناسب را انجام دهیم. در این مقاله، مراحل اساسی این فرآیند را بررسی میکنیم.
۱. شناسایی تجهیزات حیاتی
اولین قدم در راهاندازی یک برنامه تحلیل روغن، شناسایی تجهیزات مهم یا حیاتی است. نیازی نیست که برای تمام سیستمهای روانکاری شدهی کارخانه تحلیل روغن انجام شود؛ بلکه باید تمرکز روی تجهیزاتی باشد که خرابی آنها میتواند تولید را مختل یا هزینههای زیادی تحمیل کند. این انتخاب هدفمند باعث میشود منابع آزمایشگاهی و زمان نیروی انسانی به شکل بهینه مصرف شود و بیشترین بهرهوری حاصل گردد.
۲. ثبت تجهیزات در آزمایشگاه
پس از تعیین تجهیزات هدف، لازم است که مشخصات دقیق آنها در آزمایشگاه ثبت شود. این ثبت اطلاعات به کارشناسان آزمایشگاه کمک میکند تا روند تغییرات روغن و وضعیت تجهیزات را در طول زمان بهطور دقیق پیگیری کنند. همچنین، آزمایشگاهها معمولا برای هر نوع کاربرد، مجموعهی مناسبی از آزمونهای تخصصی را از پیش تعیین کردهاند، بنابراین نیازی نیست نگران انتخاب تستهای مناسب باشید.
۳. ایجاد دستورالعملهای استاندارد نمونهبرداری
کیفیت دادههای به دست آمده از تحلیل روغن به شدت وابسته به کیفیت نمونهگیری است. به همین دلیل باید یک روش استاندارد و مشخص برای برداشت نمونه تعریف شود و تیم نگهداری به خوبی در این زمینه آموزش ببیند. رعایت تکنیکهای درست نمونهگیری، از جمله برداشت نمونه از مکان مناسب و در شرایط مناسب، باعث میشود نتایج آزمایش، وضعیت واقعی سیستم را منعکس کند.
۴. نمونهگیری و تحلیل روغن
پس از نمونهگیری، باید نمونهها در کوتاهترین زمان ممکن به آزمایشگاه ارسال شوند. نگهداری طولانی مدت نمونهها میتواند باعث تغییر در خواص آنها شود و نتایج غیر واقعی به دنبال داشته باشد. تحلیل کامل و دقیق نمونههای روغن به ما اطلاعاتی دربارهی وضعیت روغن و سلامت سیستم میدهد و میتواند نشانههای اولیهی مشکلات احتمالی را آشکار کند.
۵. تفسیر نتایج
نتایج آزمایشها باید به دقت بررسی شوند تا مشخص شود که آیا اقدامی لازم است یا خیر. مشاهدهی وضعیت هشدار در نتایج لزوما به معنای خرابی فوری نیست. در بسیاری از موارد توصیه میشود که پیش از اقدام به تعمیر یا تعویض قطعات، نمونهگیری مجدد انجام شود تا از صحت نتایج اطمینان حاصل گردد. مشورت با کارشناسان آزمایشگاه در این مرحله میتواند در تصمیمگیری بهتر بسیار مفید باشد.
۶. اقدام اصلاحی و مستندسازی
آخرین گام، انجام اقدامات اصلاحی در صورت لزوم و مستندسازی کامل این اقدامات است. ثبت دقیق سوابق تحلیل روغن و اقدامات صورت گرفته نه تنها به بهبود مدیریت نگهداری کمک میکند، بلکه در مواقعی که نیاز به استفاده از خدمات گارانتی تولیدکنندگان تجهیزات (OEM) باشد، اسناد و مدارک معتبری در اختیار خواهد بود. این سابقهی مستند میتواند در مذاکرات با تامینکنندگان تجهیزات و ارائهی دلایل فنی برای مشکلات پیشآمده، نقش حیاتی ایفا کند.
نتیجهگیری
تحلیل پیشگیرانه روغن ابزاری کارآمد برای افزایش طول عمر تجهیزات، کاهش هزینههای تعمیرات و جلوگیری از توقفهای پیشبینینشده در فرآیندهای صنعتی است. با اجرای صحیح این فرآیند در شش مرحلهی ذکر شده، میتوان با صرف هزینهای منطقی، ریسک خرابیهای بزرگ را به شدت کاهش داد و بهرهوری عملیات را افزایش داد. در نهایت، موفقیت این برنامه به تعهد سازمان به اجرای منظم و دقیق آن بستگی دارد.
جهت کسب اطلاعات بیشتر به منبع این نوشته مراجعه کنید.
دیدگاهتان را بنویسید
تاکنون دیدگاهی در این مطلب ارسال نشده!