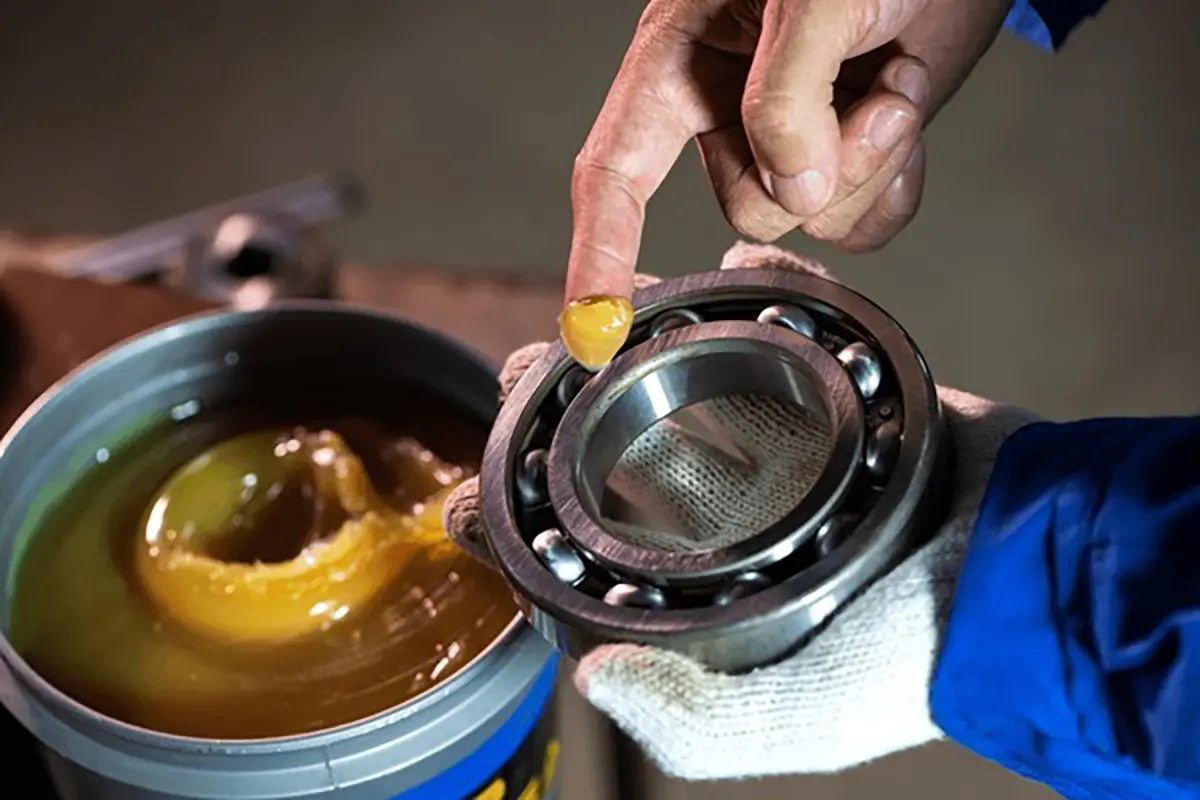
6 مرحله برای روانکاری بهینه با گریس
فهرست مطالب
برای دستیابی به یک روانکاری موثر و بدون مشکل، رعایت چند مرحله کلیدی ضروری است. در این مقاله به بررسی شش مرحله مهم در روانکاری با گریس خواهیم پرداخت.
1. انتخاب گریس مناسب
یکی از اولین و مهمترین گامها در روانکاری، انتخاب گریس مناسب برای کاربرد مورد نظر است. نوع روغن پایه، ویسکوزیته، نوع تغلیظ کننده، درجه NLGI و افزودنیهای شیمیایی، همگی عواملی هستند که باید در انتخاب گریس در نظر گرفته شوند. انتخاب نادرست گریس میتواند منجر به عملکرد ضعیف، افزایش سایش و کاهش عمر تجهیزات شود.
2. بررسی نیازهای روانکاری تجهیزات
هر تجهیز صنعتی دارای نیازهای خاصی برای روانکاری است. بررسی دفترچه راهنمای دستگاه، شناسایی نقاط نیازمند روانکاری و تعیین میزان و تناوب استفاده از گریس، از جمله اقدامات مهم در این مرحله هستند. برخی از قطعات به روانکاری مداوم نیاز دارند، در حالی که برخی دیگر تنها در بازههای زمانی مشخص نیاز به تزریق گریس دارند.
3. تمیزکاری قبل از اعمال گریس
یکی از اشتباهات رایج در روانکاری، اعمال گریس بر روی قطعات آلوده است. ذرات گرد و غبار، زنگزدگی و آلودگیهای دیگر میتوانند وارد ساختار گریس شده و خاصیت روانکاری آن را کاهش دهند. برای جلوگیری از این مشکل، قبل از اعمال گریس باید نازل های گریس کاری و سطح قطعات به خوبی تمیز شوند.
4. تعیین مقدار مناسب گریس
استفاده از مقدار بیش از حد یا کمتر از حد نیاز گریس، میتواند منجر به مشکلاتی نظیر افزایش اصطکاک، ایجاد گرمای اضافی یا کاهش کارایی روانکاری شود. بهتر است مقدار گریس مورد نیاز بر اساس توصیههای سازنده دستگاه و آزمونهای عملی مشخص شود. برای برخی از قطعات، استفاده از ابزارهای اندازهگیری میزان تزریق گریس میتواند به دقت بیشتر در این زمینه کمک کند.
5. انتخاب روش مناسب اعمال گریس
روشهای مختلفی برای اعمال گریس وجود دارد که بسته به نوع تجهیزات و شرایط کاری، میتوان از آنها استفاده کرد. گریسکاری دستی با استفاده از پمپهای گریس، روانکاری خودکار با سیستمهای مرکزی و تزریق تحت فشار، از جمله روشهای متداول هستند. انتخاب روش مناسب میتواند در کاهش هدر رفت گریس و بهینهسازی روانکاری تاثیر بسزایی داشته باشد.
6. کنترل دورهای و ارزیابی عملکرد روانکاری
روانکاری فرآیندی مستمر است و نیاز به کنترل و نظارت مداوم دارد. بررسی تغییرات در عملکرد قطعات، آزمایش نمونههای گریس برای تشخیص آلودگی و بررسی چسبندگی و یکنواختی گریس، از جمله اقداماتی هستند که به افزایش کارایی روانکاری کمک میکنند. با این کار میتوان از خرابیهای احتمالی جلوگیری کرده و طول عمر تجهیزات را افزایش داد.
برای محاسبه حجم و زمان گریسکاری به صفحه مربوط به آن مراجعه نمایید.
جمعبندی
رعایت این شش مرحله در روانکاری با گریس میتواند تاثیر قابل توجهی در کاهش هزینههای نگهداری، افزایش بهرهوری و جلوگیری از خرابیهای ناگهانی داشته باشد. انتخاب گریس مناسب، تمیزکاری قبل از اعمال، تعیین میزان صحیح، انتخاب روش مناسب و کنترل مستمر، از جمله اقدامات حیاتی در این فرآیند هستند. با پیادهسازی این مراحل، میتوان تجهیزات صنعتی را در بهترین شرایط عملکردی نگه داشت و از فرسودگی زودرس آن ها جلوگیری کرد.
جهت کسب اطلاعات بیشتر به منبع این نوشته مراجعه نمایید.
دیدگاهتان را بنویسید
تاکنون دیدگاهی در این مطلب ارسال نشده!