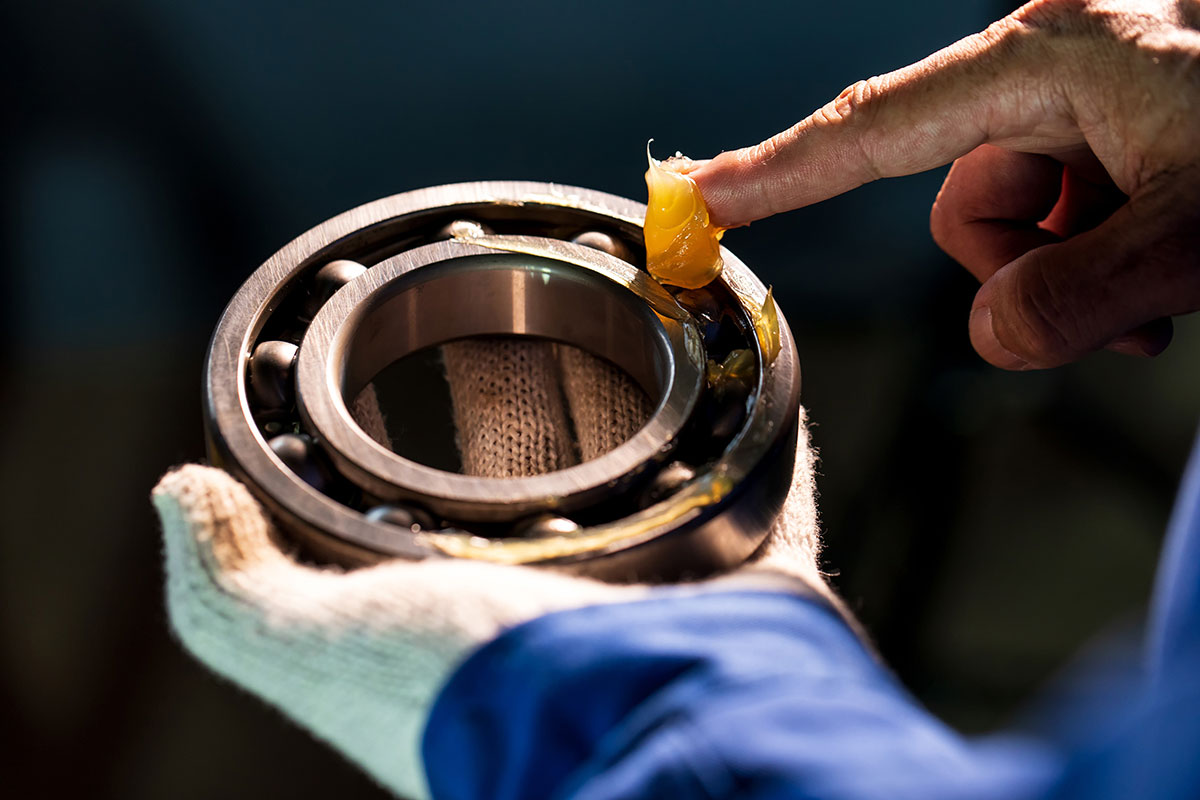
اهمیت روانکاری با گریس در افزایش عمر تجهیزات
فهرست مطالب
بسیاری از مشکلات ناشی از خرابی تجهیزات به دلیل عدم رعایت اصول روانکاری مناسب رخ میدهند. در این مقاله به بررسی جنبههای مختلف روانکاری با گریس، روشهای صحیح استفاده و نکات کلیدی برای افزایش بهرهوری میپردازیم.
۱. انتخاب گریس مناسب
یکی از اشتباهات رایج در نگهداری تجهیزات، تصور نادرست درباره گریس است. بسیاری گمان میکنند که همه انواع گریس مشابه هستند، درحالیکه هر دستگاه و شرایط عملیاتی آن نیاز به گریس مخصوص خود دارد. عوامل مهم در انتخاب گریس شامل:
- ویسکوزیته روغن پایه: برای دستگاههایی با سرعت بالا، ویسکوزیته پایین و برای دستگاههای سنگین و پرفشار، ویسکوزیته بالا توصیه میشود.
- نوع روغن پایه: گریسها میتوانند بر پایه معدنی یا سنتتیک باشند که انتخاب آنها به شرایط دمایی و عملیاتی بستگی دارد.
- افزودنیها: افزودنیهایی مانند ضد سایش، ضد اکسیداسیون و ضد خوردگی میتوانند عمر تجهیزات را افزایش دهند.
۲. تعیین محل و نحوه اعمال گریس
محل دقیق اعمال گریس در هر دستگاه متفاوت است. برخی دستگاهها دارای نقاط مشخصی برای گریسکاری هستند، اما در برخی دیگر ممکن است این نقاط مخفی یا دسترسی به آنها دشوار باشد. بنابراین، لازم است که:
- راهنمای دستگاه مطالعه شود تا همه نقاط روانکاری شناسایی شوند.
- روشی مشخص برای گریسکاری تدوین شود که شامل تعداد نقاط، نوع گریس و مقدار مورد نیاز برای هر نقطه باشد.
- ابزار مناسب برای روانکاری استفاده شود مانند پمپ گریس، ابزارهای دستی و اتوماتیک برای اطمینان از پوشش کامل سطوح.
۳. تعیین فرکانس بهینه برای گریسکاری
یکی دیگر از اشتباهات رایج در نگهداری، استفاده از یک برنامه یکسان برای همه دستگاهها است. برخی سازمانها برنامههای زمانی کلی مانند گریسکاری ماهانه یا فصلی دارند، اما این روش ممکن است برای برخی دستگاهها ناکافی و برای برخی دیگر بیش از حد باشد. تعیین بهترین فرکانس گریسکاری به عواملی مانند عوامل زیر بستگی دارد:
- سرعت و دمای عملکرد دستگاه
- سطح آلودگی محیطی
- نوع گریس و پایداری آن
- شرایط بار و فشار دستگاه
توجه به این فاکتورها باعث میشود که برنامه روانکاری متناسب با نیاز واقعی تجهیزات تنظیم شود و از مشکلات ناشی از کم یا زیاد بودن گریس جلوگیری گردد.
۴. نظارت بر عملکرد روانکاری
حتی در صورتی که بهترین گریس انتخاب شده و برنامه روانکاری بهینه تدوین شده باشد، باز هم لازم است که عملکرد گریس و تاثیر آن بر دستگاه مورد بررسی قرار گیرد. برخی روشهای نظارت عبارتاند از:
- استفاده از فناوری اولتراسونیک: این روش امکان تشخیص تغییرات در سطح اصطکاک و سایش را فراهم میکند.
- بررسی دمای قطعات: افزایش غیرعادی دما میتواند نشانهای از ناکافی بودن روانکاری باشد.
- آنالیز وضعیت گریس: بررسی کیفیت و شرایط گریس مستعمل میتواند اطلاعات مفیدی درباره عملکرد آن ارائه دهد.
۵. روشهای صحیح نمونهگیری و تحلیل گریس
آنالیز گریس روشی ارزشمند برای بررسی وضعیت روانکاری و پیشبینی مشکلات احتمالی است. برای انجام یک آنالیز موثر:
نمونهگیری باید از نقاط مناسب انجام شود تا نشاندهنده وضعیت واقعی گریس باشد.
ویژگیهایی مانند قوام، میزان آلودگی و ترکیب شیمیایی بررسی شوند تا تغییرات نامطلوب شناسایی گردند.
نتایج آنالیز در برنامههای نگهداری مورد استفاده قرار گیرد تا امکان بهبود فرآیند روانکاری فراهم شود.
برای تعیین مقدار و زمان گریس کاری، به محاسبه گر زمان گریس کاری و مقدار گریس کاری مراجعه کنید.
۶. جلوگیری از اختلاط نامناسب گریسها
یکی از علل شایع خرابی در تجهیزات، مخلوط شدن گریسهای ناسازگار است. برخی گریسها در ترکیب با یکدیگر باعث تغییرات نامطلوب در ساختار و عملکرد میشوند که منجر به از دست رفتن خاصیت روانکاری آنها میگردد. برای جلوگیری از این مشکل:
- از گریسهای سازگار استفاده شود و در صورت تغییر نوع گریس، سازگاری آن بررسی گردد.
- نقاط روانکاری بهدرستی تمیز شوند تا از باقی ماندن گریس قبلی جلوگیری شود.
- سیستمهای مدیریت روانکاری اجرا شود تا اشتباهات در استفاده از گریسهای مختلف کاهش یابد.
۷. مستندسازی و بهبود فرآیندهای روانکاری
نگهداری و ثبت اطلاعات مربوط به روانکاری نقش مهمی در بهبود عملکرد تجهیزات دارد. هرگونه خرابی باید مستندسازی شده و علت آن تحلیل گردد تا از وقوع مشکلات مشابه در آینده جلوگیری شود. برخی اقدامات مفید عبارت اند از:
ثبت دقیق اطلاعات مربوط به زمان و مقدار گریسکاری
تحلیل خرابیها و تعیین علت اصلی آنها
اجرای تغییرات در برنامههای نگهداری برای بهینهسازی فرآیند روانکاری
نتیجهگیری
روانکاری با گریس نه تنها یک فرآیند ساده نیست، بلکه نیازمند برنامهریزی دقیق، انتخاب مناسب مواد، نظارت مستمر و بهروزرسانی روشها است. با رعایت این اصول، میتوان عمر تجهیزات را افزایش داد، هزینههای نگهداری را کاهش داد و از خرابیهای غیرمنتظره جلوگیری کرد. یک برنامه روانکاری مناسب نهتنها به بهبود عملکرد تجهیزات کمک میکند، بلکه ایمنی کارکنان را نیز تضمین خواهد کرد.
جهت کسب اطلاعات بیشتر به منبع این نوشته مراجعه کنید.
دیدگاهتان را بنویسید
تاکنون دیدگاهی در این مطلب ارسال نشده!